- Blog
Accelerate supply chain performance and mitigate disruptions with circular operations
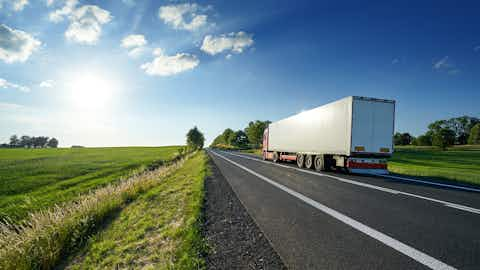
Today's supply chains are commanding the attention of boardroom decisions. And it comes to me as no surprise. Climate change, geopolitical tensions, labor crunches, and changing consumer behavior pose serious challenges to your business continuity, efficiency, and profitability. But that's not all. With regulatory policies like the Carbon Border Adjustment Mechanism (CBAM) trying to hold suppliers accountable to common environmental standards, keeping up with continuous disruptions is hard.
One solution? Rethink operational strategies to adopt a more sustainable approach based on circular principles – a model that aims to eliminate waste and pollution, circulate products and materials, and regenerate nature.
Two effective circular strategies to drive sustainable growth
Implementing circular operations isn't a solo activity – something I emphasize in every client conversation. You must collaborate with stakeholders – suppliers, customers, service providers, waste recyclers, regulators, and others – across the value chain. Plus, bring in new data sources from internet-of-things (IoT) devices and use AI technologies with advanced analytics for end-to-end supply chain visibility. All this, with robust circular strategies, will lead you to sustainable, traceable, and resilient supply chain operations.
- Repair rather than rebuild so you can deliver faster and more cost-effectively. Supply chain leaders often approach me to resolve procurement hiccups. Instead, I suggest recovering value from existing assets by strengthening aftermarket services to prolong the product life cycle. With fewer resources and less waste, you control production and disposal costs and adhere to carbon regulations by limiting energy consumption and greenhouse gas emissions – a potent way to reduce lead time, inventory, and transportation costs while increasing asset utilization and customer satisfaction.
- Move operations closer to customers through nearshoring. By shifting away from long and complex supplier and transportation networks, it's possible to mitigate the risks of supply shortages, delays, or quality issues affecting operations – I've seen this strategy work. With fewer geographical and operational steps to get a product to the customer, you can improve time to value. You can use local or regional hubs for repair or refurbishment services. But companies must be careful in adopting the right nearshoring strategy – choose locations with stable free-trade agreements, currency, and procurement laws.
From strategies to actions
I know it seems like doing the "right" thing always costs more. But what I find over and over is that investing in repair strategies returns measurable improvement in operational efficiency. Here are two examples where we partnered with companies to bring circular strategies to life:
Connected dealer inventory solution: We partnered with Terex, a global manufacturer of materials processing machinery and aerial work platforms, to reduce customer wait time for service parts. The reason? Lack of real-time inventory data at their partner dealers. We adopted an AWS-hosted global supply chain planning solution that connects its ecosystem of dealers. The client reported a 95% increase in the order fulfillment rate and an 80% reduction in planning efforts with over 1,000 service opportunities every month. A supply chain transformation in which everybody wins.
Connecting repair to quality: A renowned South Korean consumer electronics company needed more tools and processes to manage its after-sales processes effectively. Genpact shared best practices and developed key performance indicators (KPIs) to drive the performance it sought. As a result, the company reduced the overall number of repairs by 50% due to better quality and improved inventory planning across its ecosystem.
A path to circular brilliance
Continuing with linear operations perpetuates the risk of supply disruption. Finding ways to introduce circular approaches can span from circular pallets and packaging to redesigning future supply chains.
The core competencies needed to make your supply chain more circular go beyond how you operate today. Look to new partnerships, networks, capabilities, and systems to help fill the gaps in capabilities like repair process optimization, spare parts management, repair network expansion, and in-market remanufacturing. The rewards of resilience, sustainability, and innovation are huge provided you know where to begin.